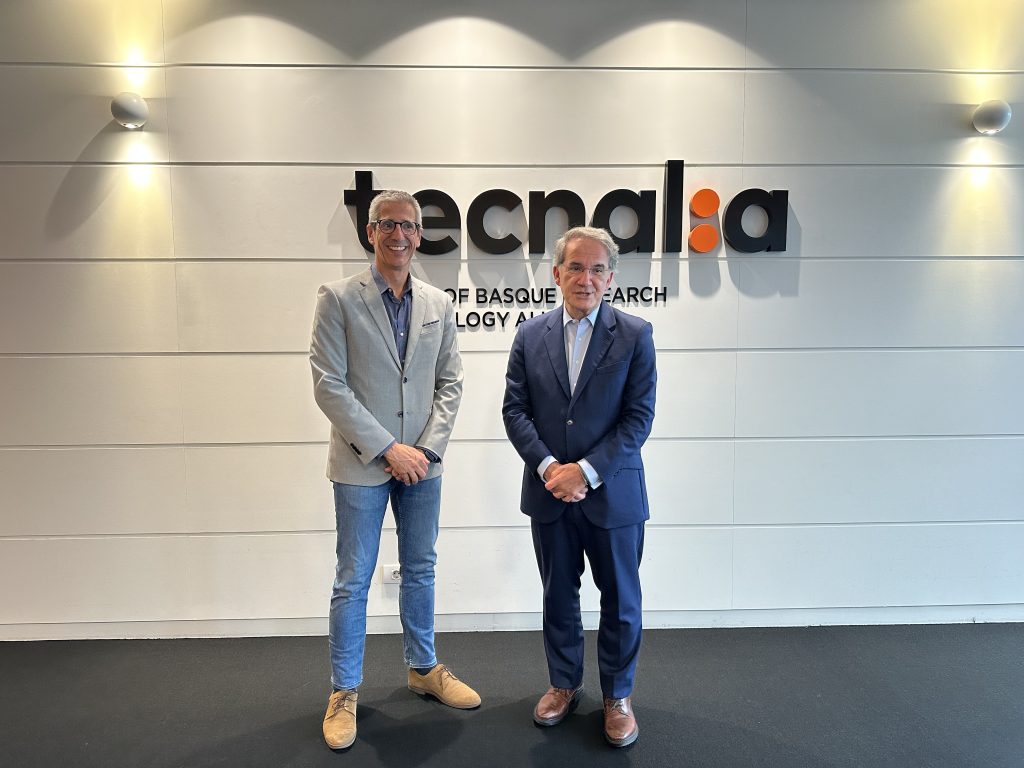
Press release
Press release
13 November 2018
The technological and innovative capacity of the TECNALIA research and technological development centre has reached the United States government, specifically the US Department of Energy’s Idaho National Laboratory (INL), for whom TECNALIA, under a subcontract with BATTELLE ENERGY ALLIANCE, LLC (BEA), is developing a new class of robots to handle radioactive materials.
The aim of the Sample Preparation Laboratory at INL, which will provide irradiated materials testing capabilities in support of nuclear reactor research development, demonstration, and deployment, is to achieve a secure and agile solution that increases productivity in its operations. Currently such operations are carried out remotely (to protect the operator) with mechanical manipulators that are difficult to control, unintuitive and have limited abilities for guiding and moving parts between different spaces and tests. The team at INL has proposed an innovative robotic solution to replace this dated technology that is cost effective and has the potential to provide the operator with greater dexterity during remote operation. With the proposed system, remotely controlled electromechanical robots accurately reproduce movements of the operator’s hands, resulting in handling that is more accurate, safe and intuitive. As a consequence, it is expected that remote handling of irradiated material samples will be faster and more efficient, leading to increased operational performance.
TECNALIA was awarded a Contract to design and implement this concept through a competitive bidding process. TECNALIA is well suited for this project because of their previous experience in developing a similar system for tele-operated, robot-assisted surgery. Following specifications defined by INL, TECNALIA has devised a novel robotic manipulator made up of two main subsystems: the first is comprised of two motorised robot arms with grippers at the end of each to handle objects within the irradiated environment (a closed “hot” cell equipped with video cameras); the second is a remote work station located in the safe zone of the facilities used by a technician to control the movement of both arms.
The novel system is designed to support both autonomous and manual operation. In the first case, the robots inside the irradiated “hot” cell can carry out automatic lift, move and place operations based on their integrated artificial-vision systems and controllers. In the second, the technician continuously guides the movements of the robot arms from the remote workstation. He or she manipulates specialised joysticks that can apply to his or her hands the same forces that the robot is applying to the objects inside the irradiated cell. This reflection of forces to the operator´s hands guarantees intuitive real-time control of the robots and of the objects being handled.
The technologies used and developed in this project have previously been applied in the medical sector to make non-invasive surgery easier. They can also be used in other environments that may be dangerous for people (due to the presence of harmful substances, etc.). Although remote handling has existed for decades using highly specialised hardware, the appearance of new-generation mechatronic robots, specialized joysticks that reflect forces to the hands and 2D/3D visualisation allows innovative approaches to these problems, promising greater productivity and flexibility at a lower cost.
Currently, the robot is in its final design stage at TECNALIA and is expected to be delivered to INL by the end of the year to support program development activities.