CIRMETAL offers solutions for eco-design and development of new metal alloys and components, decarbonisation of processes and increased circularity of materials through recycling and recovery of metals.
Achieving climate neutrality through a sustainable and resilient model is the biggest challenge facing industry today.
Where the pilot plant is located
The CIRMETAL Pilot Plant is located at TECNALIA’s location in Ir ún, where it deploys its equipment and all its processes.
CIRMETAL offers supply solutions to help you to face the energy transition
TECNALIA offers customers an industrial plant for metallurgical processes that is unique in Spain and Europe, created to develop and optimise ecological transition solutions, focusing on the value chain of raw materials.
Thanks to the extensive knowledge gained over more than twenty years of experience by its staff specialising in high temperature processes for the metallurgical industry, together with the available equipment (melting and casting furnaces with power supply up to 700kW, plasma heating, strip casting, muffles and heat treatment and thermo-mechanical furnaces, stirring systems, high pressure die casting (HPDC), crushers, presses, mills, separators and mixers), TECNALIA is a unique and essential technological partner for companies in the sector that want to innovate in materials, products and processes.
Unique plant equipment: WDXRF wavelength-of-light X-ray fluorescence analysis equipment
The plant has wavelength-of-light X-ray fluorescence analysis equipment that provides superior spectral resolution compared to energy-dispersive fluorescence. It has six diffracting crystals covering the range from boron. It is calibrated for ferroalloys, ceramics/refractories and superalloys, and also has a non-standard analysis programme. The technique allows quantitative analysis of the constituent elements of solid/powder/liquid samples.
How TECNALIA works on the metallurgical process
- TECNALIA carries out developments and research from the theoretical conception, including computational simulation, tests and characterisation in the laboratory, to the adjustment and validation of the same in industrial-scale processes.
- TECNALIA works on component eco-design solutions, the development of new metal alloys optimised for specialised and current in-service performance requirements, the decarbonisation of processes and an increased circularity of materials through recycling and recovery of metals.
- TECNALIA aims to support the metallurgical industry ecosystem in its goals of ecological transition and sustainable use of raw materials through the development of competitive, sustainable and resilient manufacturing and business models.
- TECNALIA works from a holistic perspective that encompasses the entire value chain with a strong emphasis on the circular economy.
Who we can help
- Metallurgical sector
- Metal alloy producers and processors
- Founders
- Manufacturers of metal components
- Refiners
- Recyclers
- Waste managers and waste processors
- Manufacturers of equipment and consumer goods
Why TECNALIA is the technology partner you need
If your organisation is interested in:
- (Eco)designing and developing alloys with specific properties tailored to new applications or new manufacturing processes.
- Replacing critical materials in your products.
- (Eco)designing metal components taking into account a combination of service conditions and the manufacturing process to bring lightness and sustainability to your products while adding design freedom.
- Decarbonising high-temperature industrial processes by the electrification of heating systems (induction, high power thermal plasma (HTPT), microwaves, etc.)
- Analysing the possibilities of industrial use of H2, syngas, biochar as renewable fuels with pilot plant tests.
- Increasing the percentages of recycled material used as raw material in manufacturing processes without compromising the quality and performance of the manufactured component.
- Recycling and recovering high-value metals from end-of-life (EoL) components, waste or industrial by-products.
- Optimising and increasing the efficiency and productivity of your high-temperature manufacturing processes.
- Digitalising, connecting and automating operations in your processes to reduce costs or increase quality ratios.
CIRMETAL also has a specific area to test the industrial use of new renewable alternatives focusing on the decarbonisation of industry; industrial use of H2, syngas, biochar.
Contact TECNALIA.
TECNALIA is looking forward to hearing about your issues or innovation needs, in order to work closely with you to develop competitive and sustainable solutions.
Related Laboratory Services
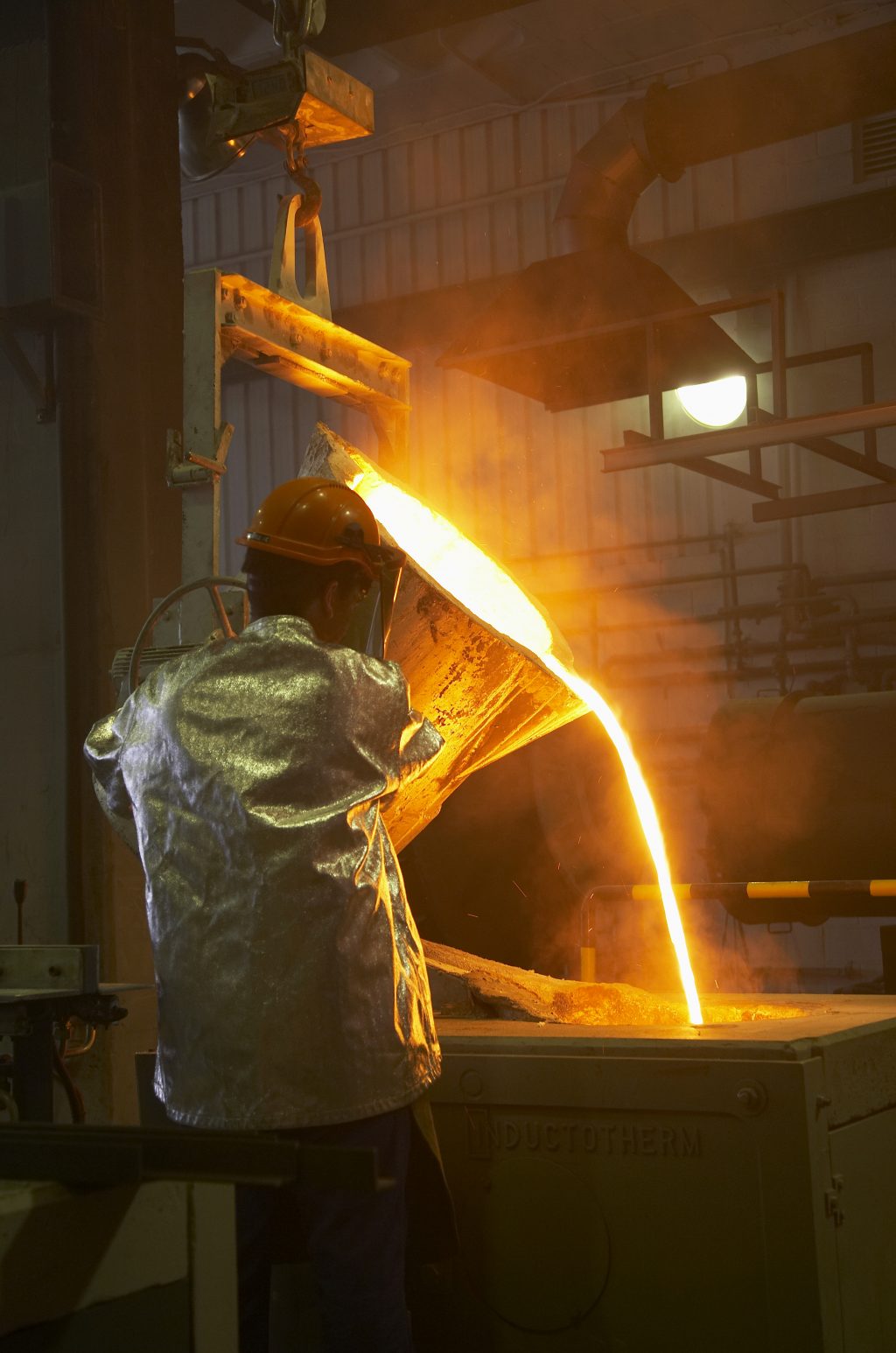